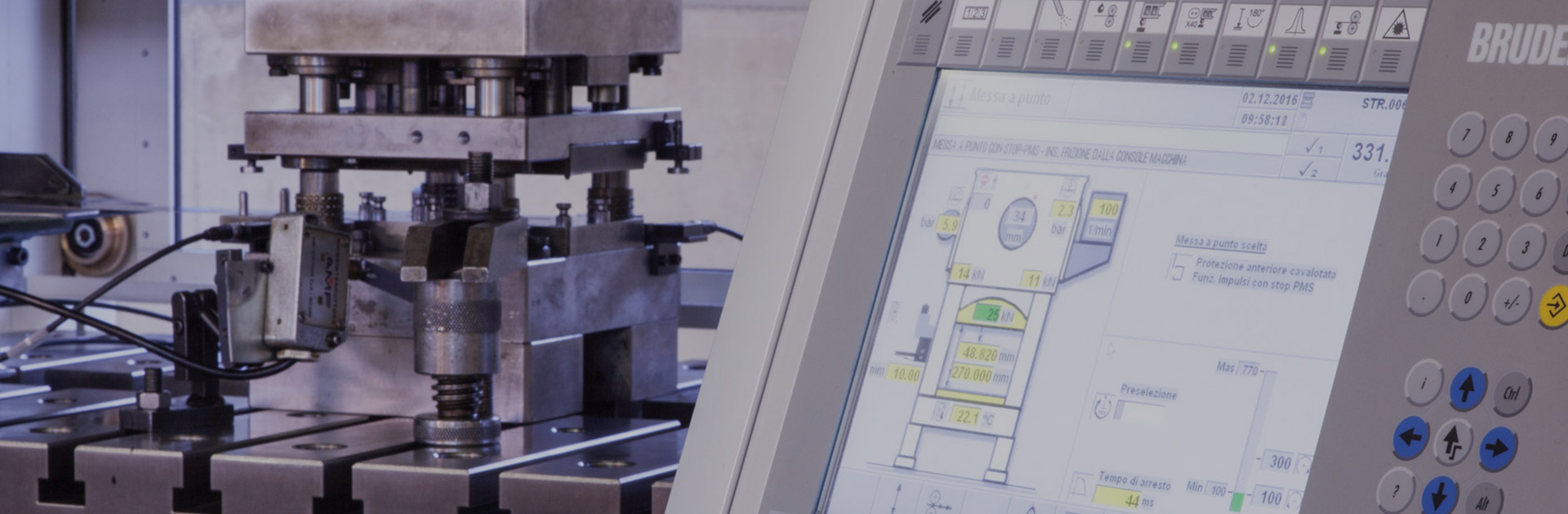
In 2016 Vito Rimoldi created an internal division specializing in the blanking of steels with a high mechanical resistance (up to 2100 MPa) and a high fatigue resistance, which has enabled the company to produce metal components, in particular reeds and valve stops for refrigeration and air compressors.
Blanking is the most commonly used technology in the production of metal components. Its use requires high-quality raw materials with specific features, great attention to the design of the mold in each of its progressive steps, the use of high-speed and high-precision presses, and a sophisticated control method.
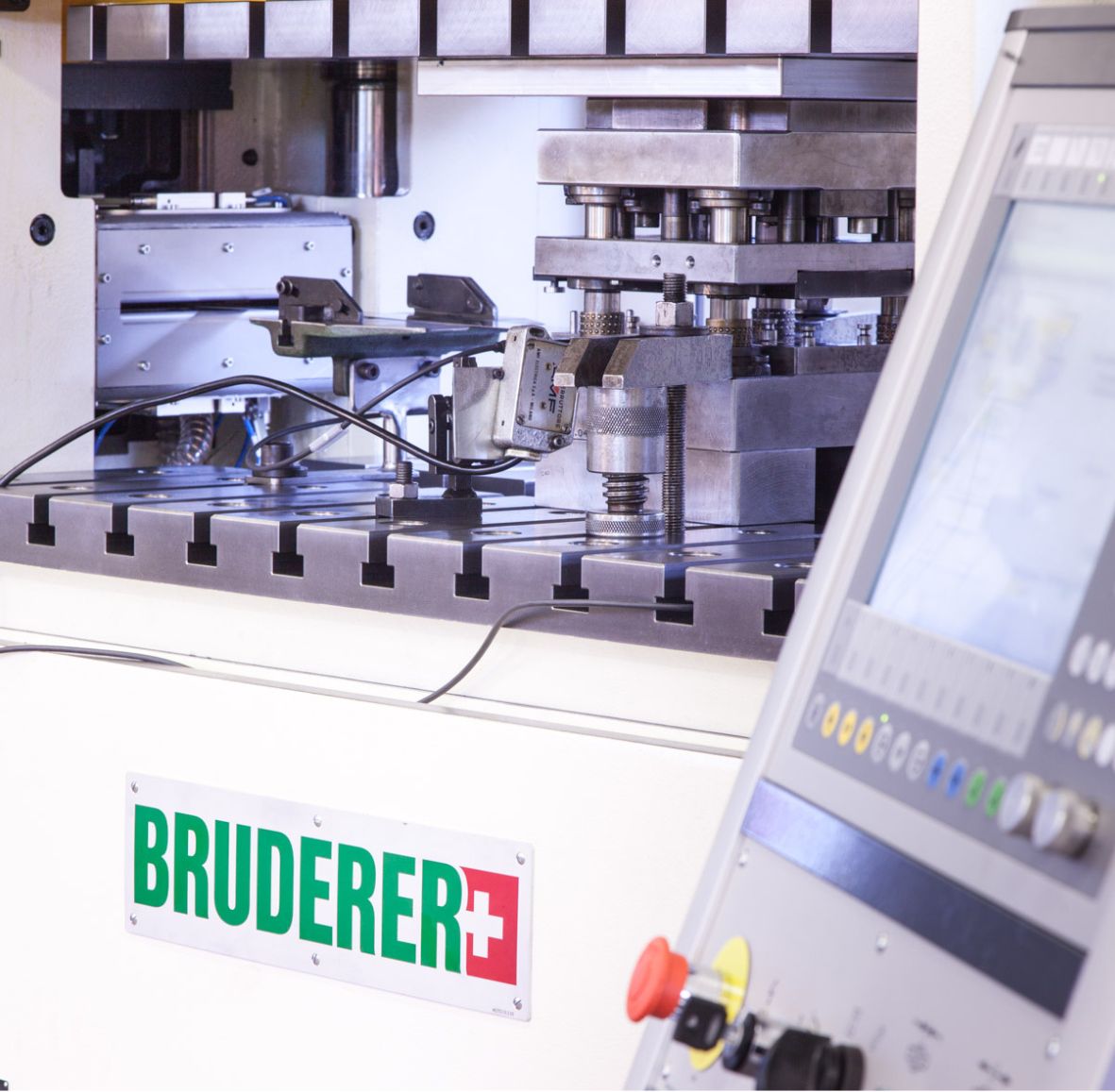
Machines and blanking dies
To create high quality and reliable products, our company uses the latest generation of blanking machines, on which we have installed sensors to control for many different parameters, such as die parallelism, pitch control, and blanking strength.
The in-depth knowledge of the relevant materials that we have gained by close collaboration with leading global suppliers allows us to choose the best production solutions and to focus on the most critical aspects of the process.
Blanking dies are crucial elements of the blanking process; the design of the dies and the high quality of our production are fundamental to guaranteeing the replicability of our processes.
High-quality components
In the blanking process, a perfect synergy of complex variables (such as materials, the geometry of the parts, productivity, and cutting quality) must be well controlled.
Thanks to our experience with materials and geometries we are able to reduce the number of issues that affect our products. During the blanking process, constant monitoring of blanking parameters is essential, including the precision of the applied cutting force and maintaining the flatness of the parts.
Blanked parts are used in harsh environments, where reliability and fatigue resistance are keys to success. Moreover, dimensional accuracy must be maintained within a few microns.