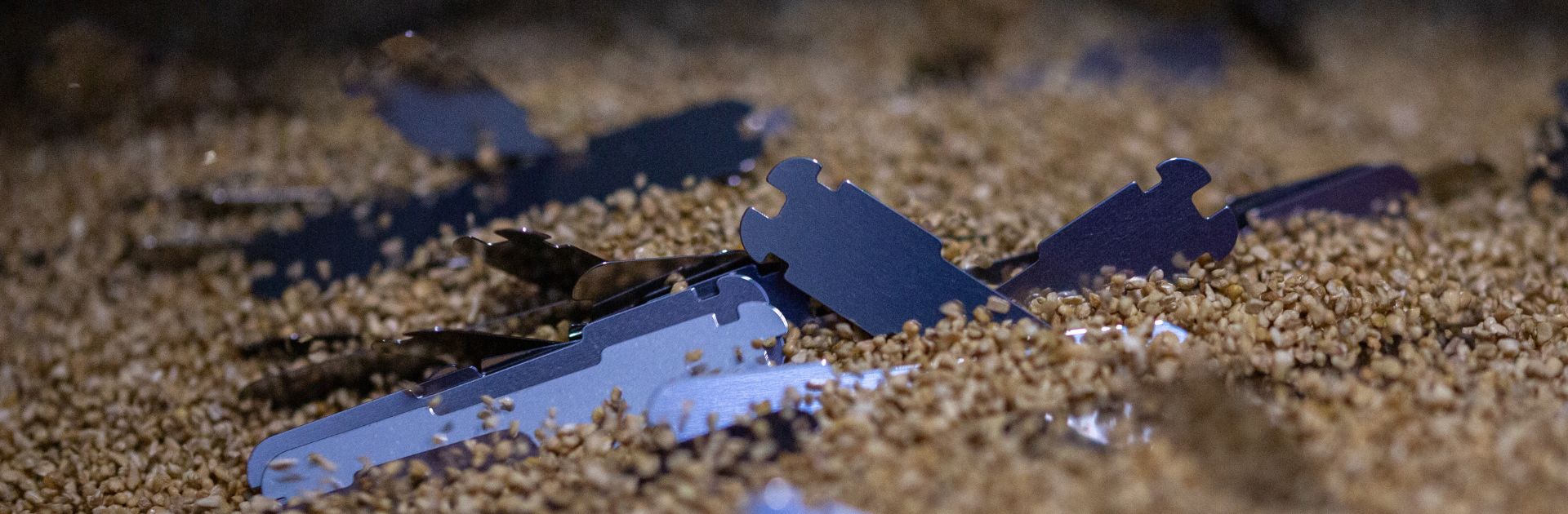
Vito Rimoldi S.p.A. uses the appropriate blanking techniques for particularly tough metals; we take care of dies design and manufacturing and can effortlessly carry out the blanking of large production series. Furthermore, the dies are equipped with special sensors that allow instantly locating any defect and measuring the repeatability of the process.
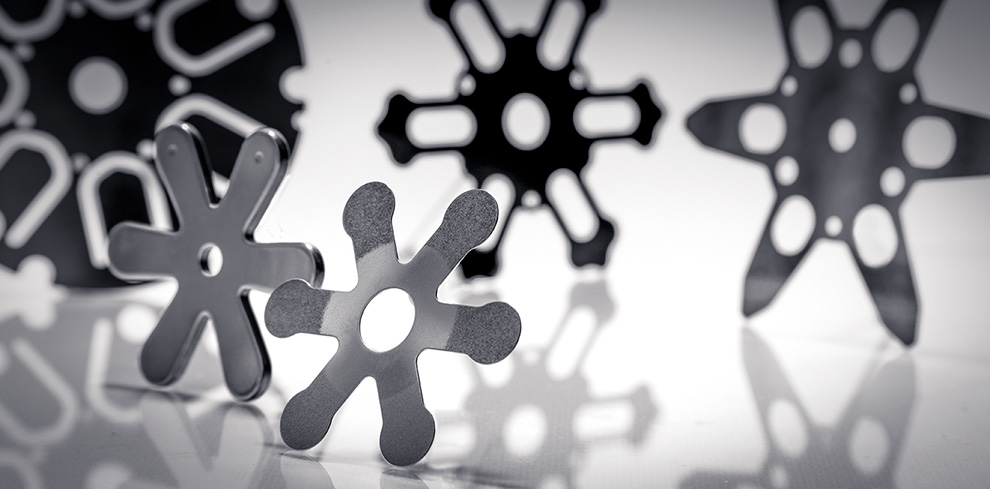
The mechanical components subjected to fatigue must be correctly designed and machined, so that each section of their surface is free from any critical persistant slip band that may cause cracks. The lack of such defects significantly increases their duration and fosters extremely high resistance levels, especially if the stress is applied in a cyclic and continuous manner.
All the stages of the process become critical, without exception, starting from the blanking, whose characteristics should prevent any "flaw" in the material right from the start. A seemingly easy stage, at least from a conceptual perspective, which should still take into consideration complex variables, such as the materials (hardness, tenacity, lamination direction), the geometry of the component to be obtained (thickness, length of the profile to be blanked, bending), productivity and the characteristic of the blank (depth and rip). For this reason blanking means defining a process that includes the study of the material, the design of the die and its progressive stations, the use of a machine that is suitable to carry it out as well as the implementation of a suitable control method. Each variable must then be fully controlled, thereby making a process which is by nature suitable for mass production, repeatable. All this to get a cut feature always extremely "clean" with a reduced presence of discontinuities.
But blanking cannot guarantee by itself the resistance to fatigue because, although reduced to the lowest terms, the presence of flaws that trigger cracks persists. For this reason finishing is a complementary process that involves removing any imperfection caused by cutting as well as those that are present on the surface of the components. This process is apparently trivial, but requires instead some careful considerations to define the parameters and the technology to be used to remove defects, the abrasive materials, the components to protect the steel from chemical attacks and oxidation, the timing for finishing and the number of components to be treated at the same time. All such variables must be measured and monitored to make processing stable and to ensure the result is repeatable.
What sets us apart
- We know the material technology which is suitable for use in conditions of particularly heavy cyclic fatigue.
- We are expert in block die and progressive die design and techniques.
- We design and manufacture the dies, ensuring that they are optimized for each application in terms of dimensional accuracy and efficiency in the use of the raw material.
- We use the correct blanking techniques for especially tough metals.
- We are able to carry out the blanking of large production series without any problems.
- We use the best punching presses on the market (punching presses by Bruderer & Dobby Yamada).
- Our dies are fitted with special sensors that allow us to instantly locate any defect and measure the repeatability of the process.
- We check components at the start of production, during the production stages on board the machine and at the end of the blanking process.
- We establish the best finishing process by identifying the method, the technology, the abrasive materials and the parameters
- We conduct all the necessary tests to verify the results and ensure the repeatability of the processes.
- We conduct the inspections and we check the measurements agreed with the Customer to allow "free pass" supplies (documentation included).
- We can pack finished products using methods and in quantities that are suitable for use with automatic assembly machines.
- We track the full productive cycle of materials, processes, in-line checks and operators authorised to carry out the activities, providing the Customer with the information, when requested.
- Thanks to our innovative cutting solutions and to the possibility of carrying out surface treatments in our premises, we guarantee extremely fast prototyping and supply of small pre-series.