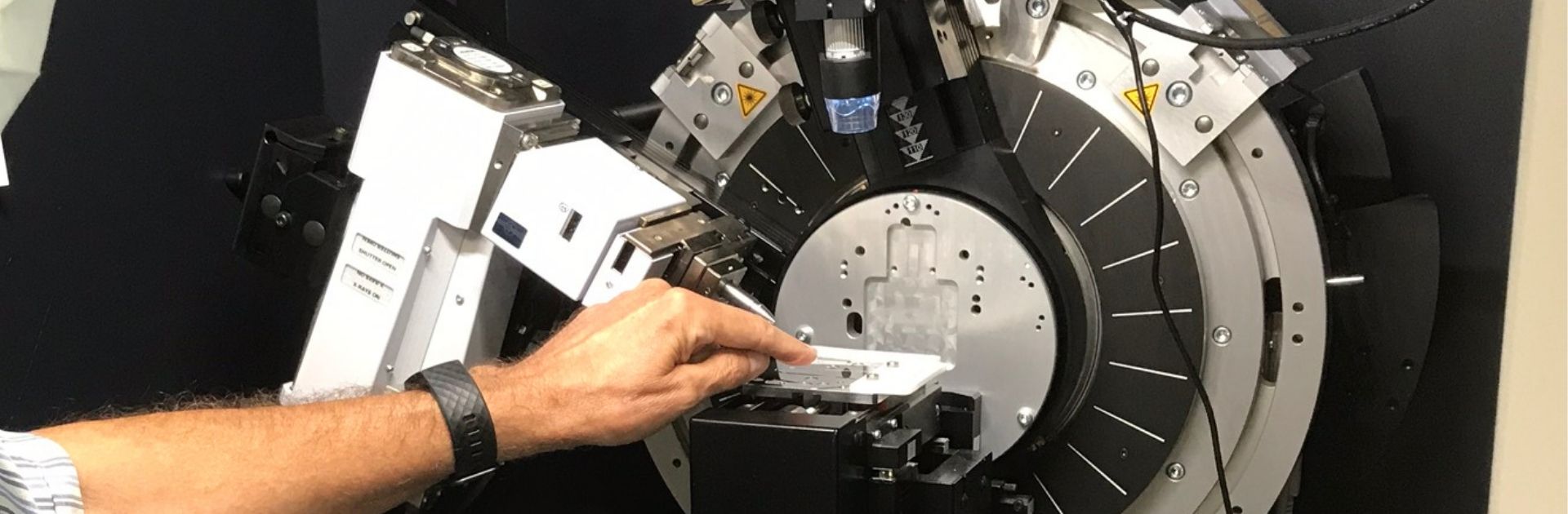
Customized finishing processes
The flapper valves are the most heavily stressed components in compressors for cooling systems.
A long life durability of compressors is therefore linked to the fatigue resistance of the flapper valves themselves, and the use of hardened steels, specially developed for such heavy working conditions, may not be a sufficient measure.
Accurate finishing treatments, which eliminate every possible microcracks sources, and the application of an external compressive stress (“residual stress”), are the key factors for fatigue resistance maximization.
To obtain the maximum performance from valves, precise and standardized tumbling processes are needed, with custom-made receipts, carefully studied to satisfy the requirements of each customer.
That’s why our R&D Department has been working for some years with the best Italian University Centers studying the residual stress level achievable on flapper valves and the optimization of the relevant production processes.
Through the tumbling we are able to obtain up to 100 MPa increase with respect to the starting material properties.
We continually deepen our technical knowhow to make the relationship with our customers more and more effective.
To punctually measure residual stress we purchased a highly valuable instrument, a diffractometer manufactured by the German company Bruker.
The instrument works by emitting X-rays beams, that is a spectrum of electromagnetic radiation capable of penetrating bodies that are opaque to ordinary light: these rays allow to investigate the internal features of the steel, its microstructure and inter-crystalline distance.
After the tumbling, the steel that makes up the valves is hardened, that is, is made more resistant.
With the diffractometer we are able to measure the level of this resistance as it is detectable from the variation of the inter-crystalline distance of the steel itself, compared to its theoretical structure, which is regular, made of equidistant crystals.
Usually, the measurement of residual stress is performed in a well-defined area of the valve, which corresponds to the area subjected to the maximum stress state.
Since there is a correlation between the X-ray measurements and the surface compression state present on the valve, we are able to translate the measurements into a compression value, expressed in Megapascals.
In this way we produce certified measurement tests of the residual stress present on our valves, creating solutions that meet the specific requests of our customers.