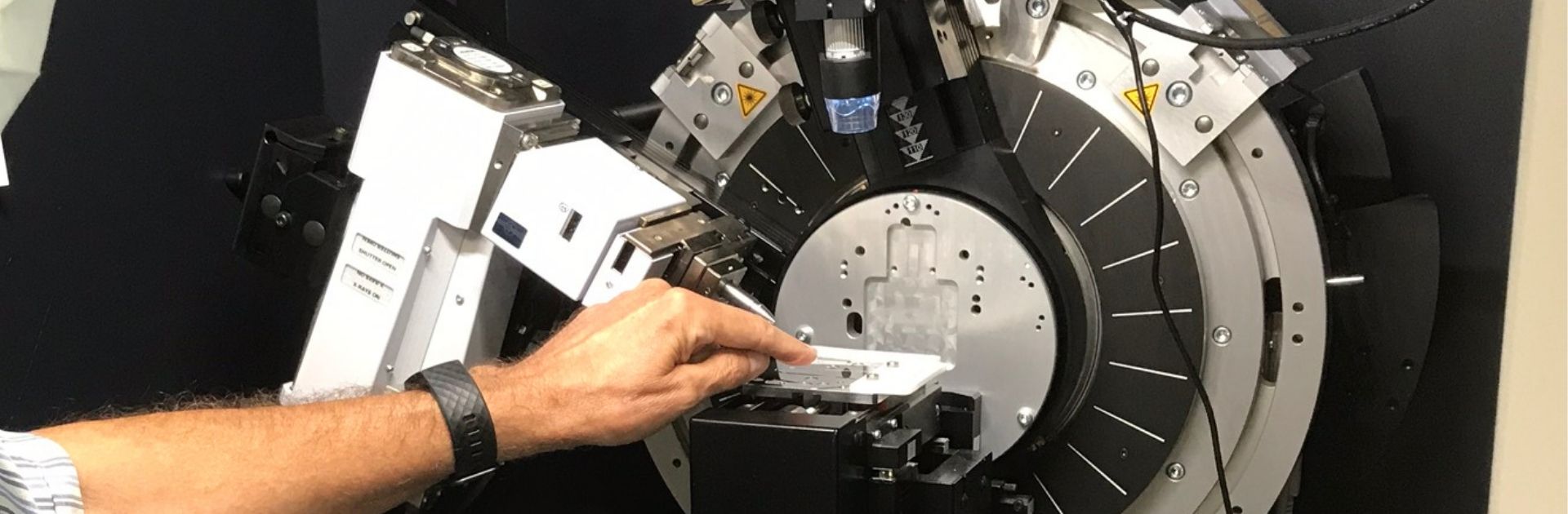
Processi di finitura customizzati
Le valvole lamellari sono i componenti più sollecitati nei compressori frigoriferi. La durata di un compressore è strettamente legata alla resistenza a fatica delle valvole stesse e, in condizioni di lavoro gravose, l’utilizzo di acciai speciali può non essere sufficiente.
Gli elementi fondamentali per la massimizzazione della resistenza a fatica sono un’accurata finitura superficiale, che eviti possibili fonti d’innesco a rottura, e l’applicazione di uno stato tensionale superficiale di compressione (“residual stress”).
Per ottenere il massimo della performance dalle valvole sono necessari processi di burattatura precisi e codificati, con ricette ad hoc, accuratamente studiate per soddisfare i requisiti specifici di ciascun cliente.
Proprio per questo motivo, il nostro ufficio R&D collabora da anni con i migliori centri di ricerca universitari italiani allo studio dei livelli di stato tensionale superficiale raggiungibili nelle valvole e all’ottimizzazione dei processi produttivi che li determinano.
Attraverso la burattatura siamo in grado di ottenere fino a 100 MPa di incremento rispetto alle proprietà del materiale di partenza.
Approfondire la competenza tecnica e la conoscenza delle applicazioni è il nostro modo di rendere efficace il rapporto con la Clientela.
Per misurare in modo puntuale lo stress residuo abbiamo inoltre investito in una strumentazione all’avanguardia, dotandoci di un diffrattometro prodotto dall’azienda tedesca Bruker.
Lo strumento funziona emettendo un fascio di raggi X, cioè uno spettro di radiazioni elettromagnetiche in grado di attraversare corpi opachi alla luce ordinaria: questi raggi consentono di indagare la struttura e la microstruttura dell’acciaio attraverso l’identificazione della distanza inter-cristallina presente nel materiale attraversato.
A seguito della burattatura, l’acciaio che costituisce le valvole viene incrudito, cioè reso più resistente.
Con il diffrattometro siamo in grado di misurare l’entità di questo incremento di resistenza in quanto è rilevabile nella variazione della distanza inter-cristallina dell’acciaio stesso, rispetto alla sua struttura teorica, che è regolare, fatta di cristalli equidistanti.
Solitamente la misurazione dello stress residuo viene eseguita in una zona ben definita della valvola, che corrisponde all’area sottoposta al massimo stato tensionale.
Poiché esiste una correlazione tra le misurazioni effettuate con i raggi X e lo stato di compressione superficiale presente sulla valvola, siamo in grado di tradurre le misurazioni in un valore di compressione, espresso in Megapascal.
In questo modo produciamo prove di misurazione certificate dello stress residuo presente sulle nostre valvole, creando soluzioni che incontrano le richieste specifiche dei nostri clienti.