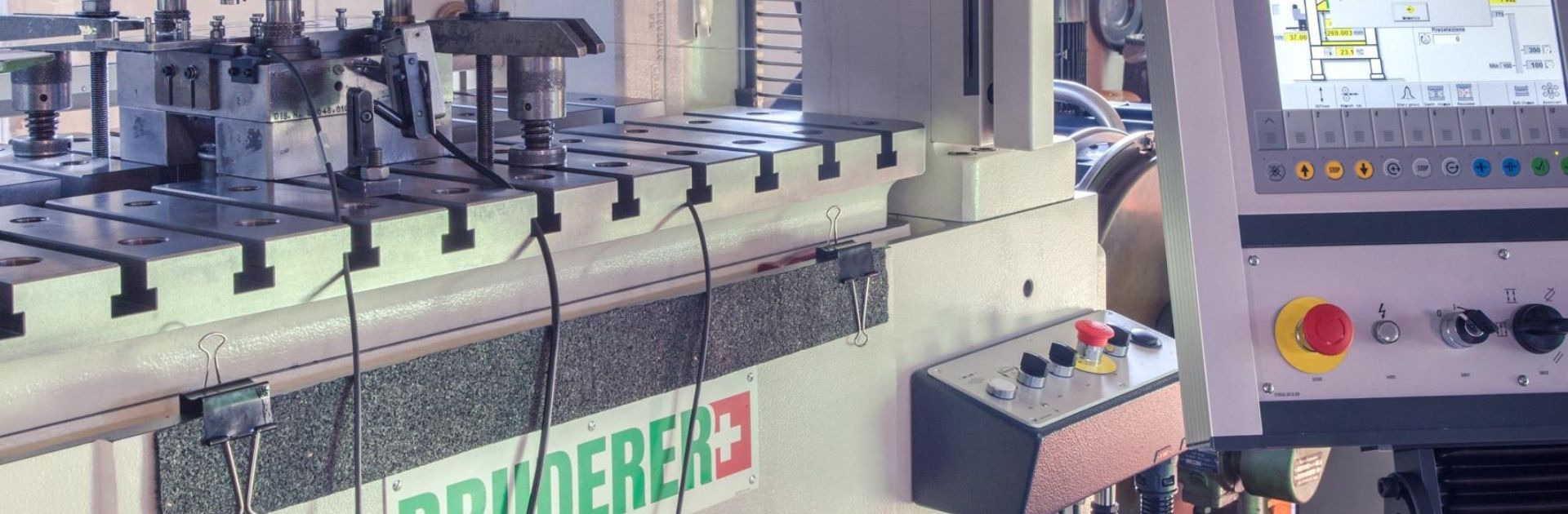
The blanking technique of hardened and tempered steels
Vito Rimoldi specialises in the blanking techniques of high mechanical strength steels (up to 2100 MPa) and high fatigue strength.
In this process it is essential to take care of complex variables, such as: materials, geometry of the component to be obtained, productivity, and characteristics of the blank.
For this reason, blanking is a technological process that requires suitable machines: Bruderer punching presses are synonymous in maximum performance, utmost precision, and unsurpassed reliability.
Our company has embedded a number of sensors in these machines to monitor several parameters.
The adoption of state-of-the-art internal monitoring systems favours a continuous improvement in our products quality.
Checking molds parallelism
To check the planarity of the head of the mold with respect to the die, special pairs of sensors are applied to these molds: they are a reading sensor, which is located inside the die, and a metal element which is located on the head.
The metal element is adjusted during the machine set-up phase, and is able to set up the planarity of the mold during the first strokes of the press. The values recorded in this phase act as a planarity parameter: the range of deviation from the nominal value can only be a few hundredths of a millimeter, then the machine gives an alarm and stops.
Very high precision monitoring is guaranteed by this control.
Step control Sensor
In case of simple molds, but especially in that of progressive ones, damage can be caused by a feeding error to the entire production batch. The advancement of the flat sheet metal is checked by a step control sensor installed on the mold. When a problem is detected, the sensor stops the machine.
Blanking force control
The monitoring of the blanking force constitutes a further control during the production phase. This is obtained through force sensors applied on the uprights of the machine.
In this case an initial calibration is made, and in the case of a value moving aside from the established range, the system gives an alarm.
In high-speed precision blanking processes, this type of control is very important: an increase in force, in fact, can be caused by the imperfect condition of the blanking parts, or by the presence of blanking scraps.
Without monitoring the blanking force, the defective pieces could only be found at the end of production.
Sound sensor
In addition to planarity sensors, step advancement sensors and blanking force sensors, our punching presses are also equipped with a sound sensor. This detects the intensity of the sound during the blanking phase: an acoustic variation signals that the machine is cutting abnormally and therefore it identifies a problem such as the chipping of a punch or of a die.
An acoustic reference point is also set in the initial phase: when the sensor detects values that go beyond the defined parameters, the press goes into alarm and stops immediately.